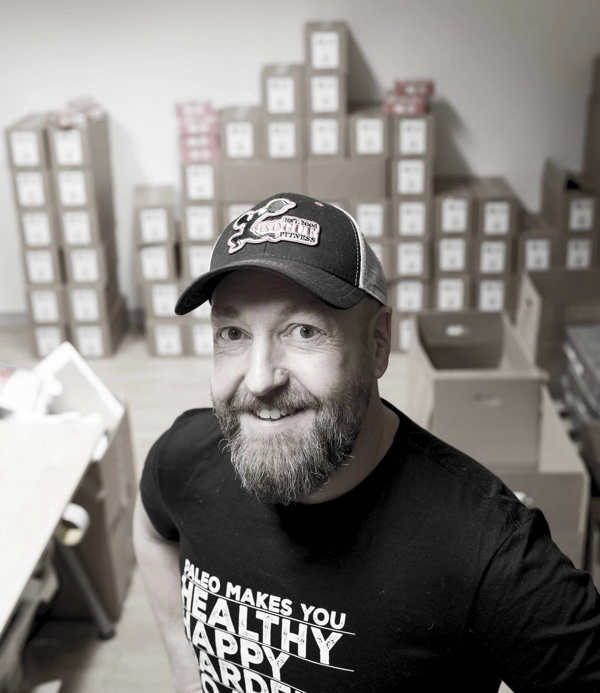
Implementing a Digital Returns System
Implementing a Digital Returns System A Project Manager's guide to business-centric success: Implementing Inretrn's leading solutions for digital returns can be a game-changer for your e-commerce...
Ever wonder what happens to products after they’re returned, repaired, or recycled?
That’s reverse logistics in action.
It’s the behind-the-scenes magic that starts once a product leaves the customer’s hands.
Think of it as logistics in reverse.
While forward logistics is all about getting products to customers, reverse logistics is about handling returns, repairs, or making sure items get a second life—whether they’re resold, refurbished, or recycled.
Reverse logistics is the process of moving goods from their final destination (the customer) back to the seller or manufacturer.
It covers activities like returns, repairs, recycling, and even dealing with surplus inventory.
For example, when a customer returns a pair of shoes that didn’t fit, reverse logistics steps in. The shoes are sent back to the warehouse, inspected, and then a decision is made—should they be resold, repaired, or recycled?
With the rise of eCommerce, reverse logistics has become even more important. Customers are returning products at much higher rates—up to 30% of online purchases get returned, compared to only about 10% for in-store buys.
There’s more to reverse logistics than just returns. Here are the main types:
Each type of reverse logistics plays a key role in maximizing value and reducing waste.
The 5 R’s capture the essence of reverse logistics:
These 5 R’s help businesses reduce waste and squeeze as much value as possible from each product.
Reverse logistics isn’t just about dealing with returns—it can be a game-changer for your business.
Here’s how:
With the right system in place, reverse logistics can turn what looks like a loss into a win—for both your bottom line and the planet.
While the benefits are clear, reverse logistics does come with its own set of challenges:
Despite these challenges, businesses that invest in smart reverse logistics solutions (like ours) can streamline the process and even turn it into a competitive advantage.
Implementing a Digital Returns System A Project Manager's guide to business-centric success: Implementing Inretrn's leading solutions for digital returns can be a game-changer for your e-commerce...
The second-hand market isn’t slowing down—it’s only getting bigger. And now, it’s got a new name: recommerce. Whether it’s reselling your favorite jacket or upcycling that old chair in...
Book your demo Fill in your details and we will be in touch and look forward to showing you our service! Book you personal demo