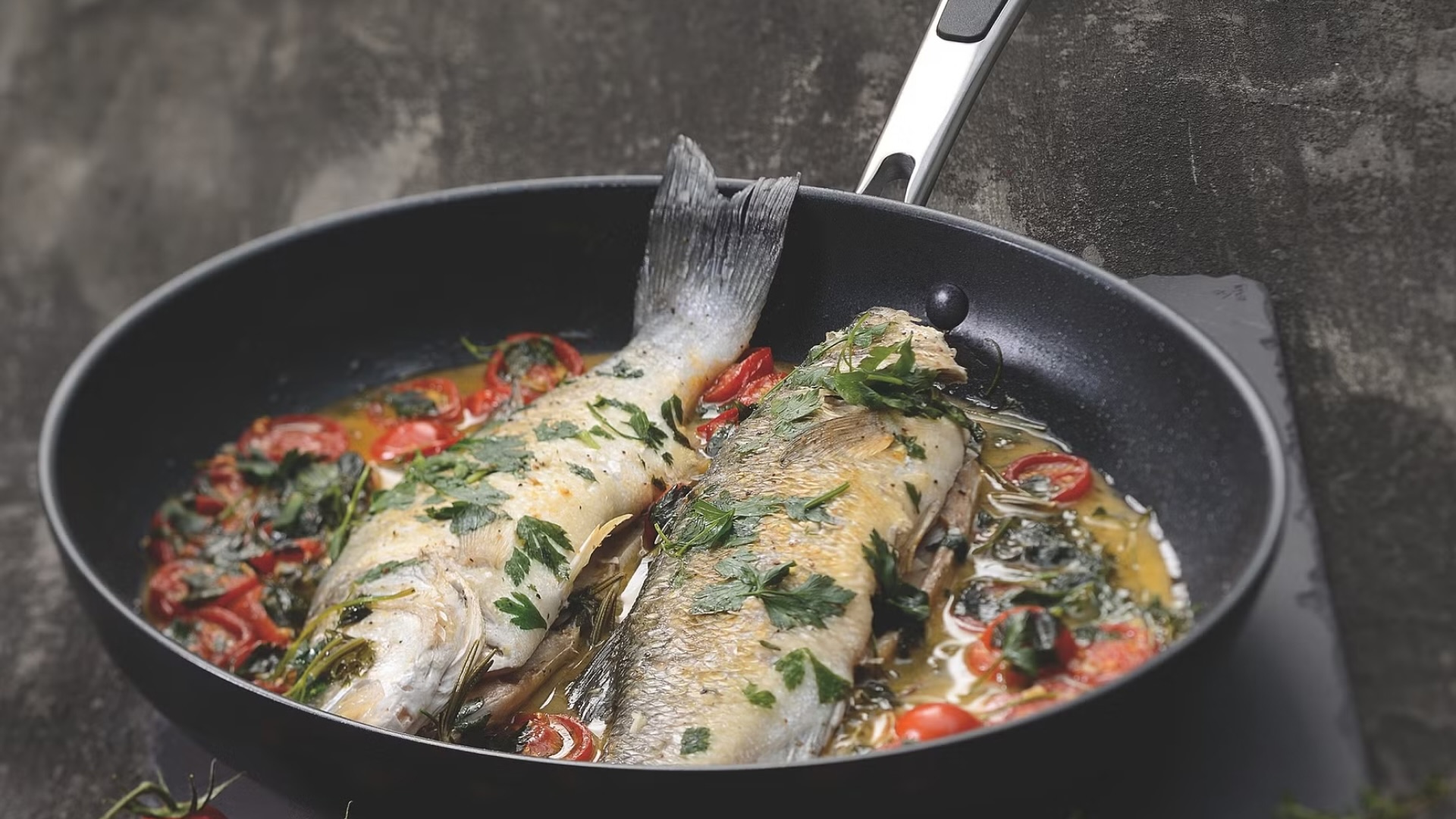
Bagaren och Kocken
Too good to be true? Not for Svenskt Tenn when digitizing their return management. They moved from a cumbersome manual process spread across multiple systems and departments, where handling a return averaged 240 minutes, to an automated digital system that has reduced the time to just 20 minutes.
With a unique range of products like mouth-blown glass and customized sofas, Svenskt Tenn faced understandable challenges in managing returns or claims. Accurate decision-making in these processes required extensive product knowledge, which wasn’t always a strength of the warehouse staff. The company realized that the lack of centralized product knowledge and gaps in current processes often led to decisions based on individual judgment, resulting in inconsistencies and undue pressure on employees. Recognizing this, Svenskt Tenn felt a pressing need to centralize their product expertise and streamline their return processes.
“We wanted to improve our digital processes, enhance our knowledge base, and thereby further improve the customer experience” – Filip Costelius, Logisics Manager
The onboarding team was outstanding, maintaining clarity and adherence to our plan throughout. Inretrn also suggested improvements to our ERP, which we adopted, resulting in even greater efficiency in our system.
Filip Costelius, Logistics Manager
Following an extensive assessment of various return management platforms, Svenskt Tenn decided on Inretrn.
Svenskt Tenn faced the complexity of managing products like sofas with customizable fabric options, which were sold as separate items but returned as a single unit, adding layers of complication to their process. It was crucial for their chosen solution to seamlessly integrate with Svenskt Tenn’s existing ERP, a requirement Inretrn was well-equipped to meet.
In collaboration with Inretrn, Svenskt Tenn crafted a strategy to address and efficiently overcome their previous challenges. Alongside a third partner, Navipro, this vision was developed into a detailed project plan. The project led to the smooth integration of the new platform with Svenskt Tenn’s systems. Once operational, they moved to automate the entire warehouse flow, enhancing overall efficiency.
One of the best things about Inretrn is that you can manage and administer so much yourself without needing to involve support.
Filip Costelius, Logistics Manager
With a new digital returns platform in place Svenskt Tenn has been able to reduce the total time to handle a return from 4 hours to only 20 minutes. This by having a digital knowledge base controlled by customer service through the platform, reducing the risk of errors. Svenskt Tenn did not only address their return management challenges but also created a more efficient and customer-focused operation overall. Svenskt Tenn are continuously developing and adding features to their platform.
“ Our aim is to actively leverage the insights provided by the platform. Our next step involves sharing profitability insights with our purchasing department. This will help ensure product quality, reduce costs, and inform our future ordering strategies.” – Filip Costelius, Logistics Manager, Svenskt Tenn